Bridging the Gap: How Textile Industry Leaders Can Transition into Smart Fabric Manufacturing π
Bridging the Gap: How Textile Industry Leaders Can Transition into Smart Fabric Manufacturing π
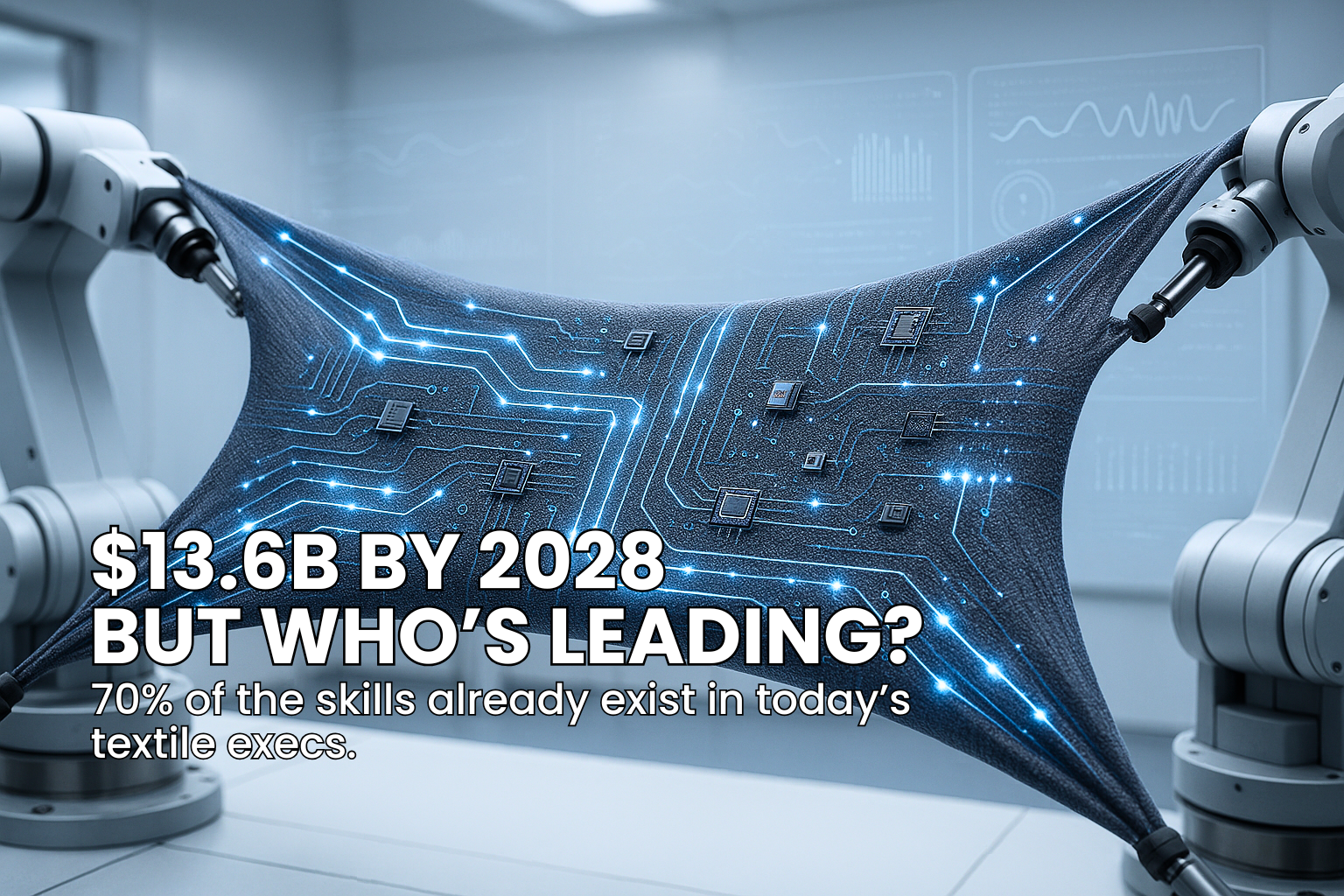
The textile industry is entering a transformative era. As smart fabrics and wearable technologies continue to grow in influence, traditional manufacturers are facing both a challenge and a significant opportunity: how can experienced textile executives successfully transition into this fast-evolving, tech-enabled sector?
At
Wyman Bain, we specialise in research-led executive search and market intelligence across the manufacturing and technology landscapes. Drawing on recent market mapping projects, we have developed a strategic framework to support textile leaders and the organisations seeking them in navigating this critical shift.
π The Opportunity: Smart Fabrics on the Rise
The global smart textile market is expected to reach $13.6 billion by 2028 (up from $3.1 billion in 2022, CAGR 28.6%*). In the UK, innovation in healthcare, sport, defence and consumer sectors is being powered by wearable tech and smart clothing.
However, there remains a shortage of leaders with both traditional manufacturing expertise and a working knowledge of smart technology. This presents a clear opportunity for forward-thinking executives to lead in this space.
π§© Executive Competency Mapping: Where Experience Meets Innovation
Our research indicates that 60 to 70% of the core capabilities needed for success in smart fabric manufacturing are already present within experienced textile leaders.
Traditional Textile Skills | Transferable to Smart Fabrics? | Additional Skills Required |
---|---|---|
Manufacturing Operations | β | IoT and Electronics Integration |
Quality Control | β | Advanced Materials Testing |
Supply Chain Management | β | Technology Vendor Partnerships |
Regulatory Compliance | β | Device Certification (CE, FDA) |
Team Leadership | β | Managing Cross-functional Tech Teams |
Key Insight: More than 80% of executives placed by Wyman Bain in adjacent manufacturing sectors over the past 12 months have successfully transferred their existing capabilities while upskilling in technology integration.
π§ Three Pathways to Transition
Based on our market intelligence, we recommend three strategic routes for executives considering a move into smart fabrics:
1. Internal Innovation Route (18 to 24 months)
Lead smart fabric initiatives within your current organisation by leveraging internal networks and resources.
2. Strategic Partnership Bridge (12 to 18 months)
Create collaborations between traditional textile firms and emerging smart fabric businesses to build dual-sector experience.
3. Direct Industry Leap (6 to 12 months)
Enter the smart fabric sector directly, often through interim or consultancy roles that allow rapid credibility building.
π Key Areas for Skill Development
To succeed in this evolving market, executives should focus on:
- Technical Integration – Understanding the fundamentals of conductive threads, sensors and microprocessors
- Digital Manufacturing – Familiarity with Industry 4.0, IoT systems and data-driven production
- Regulatory Insight – Navigating dual compliance requirements for both textile and electronic products
- Partnership Management – Collaborating with tech suppliers, software developers and innovation hubs
- Market Knowledge – Identifying smart textile use cases across health, sport and defence sectors
π Wyman Bain Insight: Over
70% of successful candidates in smart manufacturing roles (2024–25) completed at least one executive education course in digital manufacturing or IoT.
π€ Networking: The Hidden Catalyst
More than 60% of executive placements in emerging sectors happen via direct industry networking, not traditional job listings.
We recommend executives:
- Attend major wearable technology conferences such as Wearable Technology Show and Smart Fabrics Summit
- Connect with academic institutions and R&D bodies
- Seek cross-sector mentorship from innovation leaders
πΊοΈ Implementation Roadmap
Phase 1: Foundation (Months 1–3)
- Enrol in executive education programmes
- Attend key industry events
- Begin focused professional networking
Phase 2: Competency (Months 4–9)
- Upskill in technical and regulatory areas
- Lead pilot projects within your current remit
- Deepen knowledge of compliance and digital tools
Phase 3: Transition (Months 10–18)
- Explore senior roles within the smart fabrics ecosystem
- Use new connections to identify strategic career opportunities
π Why This Matters – For Companies and Candidates
The demand for leaders who can bridge traditional manufacturing with smart innovation is accelerating. For businesses, attracting these hybrid executives will be critical to staying competitive. For individuals, this is the moment to build new skills and broaden networks before the talent gap widens.
At
Wyman Bain, our transparent, research-led approach makes us ideally placed to guide both companies and candidates through this pivotal transition.
π Ready to future-proof your leadership or hiring strategy?
Visit
wymanbain.com or call us on
0203 907 7730.
Wyman Bain
Executive Search | Market Intelligence | Leadership Consulting
π London & Bristol | π
www.wymanbain.com